Inventory management is a big part of Operations Management. Not only does the quantity of inventory moving through a system affect various business costs and savings, but it also affects customer lead times, and therefore customer experience. So, does having more inventory mean faster or slower customer lead times? In this article we’ll discuss the factors affecting lead times using a traffic and toll-road analogy any how we can use Little’s Law.
If you order a new car with customised extras, such as your own specific paint colour, unique style of leather seats etc., you can’t expect a manufacturer to have that in stock ready to give you. However, you won’t want to wait months and months either for them to make it.
Likewise, if you’re eating out and you order a thin pepperoni pizza with extra jalapenos – just the way you like it, you wouldn’t expect the restaurant to have cooked a huge batch at the beginning of the day, hoping they would sell them later. You want your pizza cooked fresh for you. However, on the flip side, the speed of delivery is very important and valuable to you as a waiting customer.
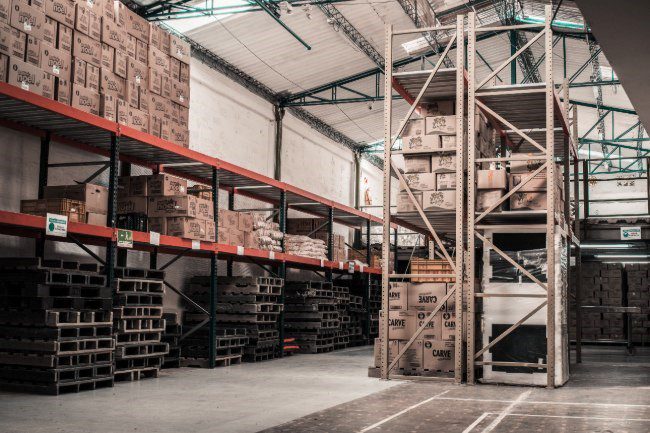
How Does “Work in Progress” Affect Lead Times?
The quantity of ‘Work In Progress’ inventory (WIP) we have moving through the system is a key determinant of a system’s “throughput-time” (the time it takes an individual item / job to go from start to finish through the system). In the car factory, the quantity of WIP would be the number of cars on the production line at any moment in time and in the pizza restaurant it is the number of pizzas the kitchen is preparing and cooking simultaneously. The throughput time is the main factor contributing to the customer’s “Lead Time” (The time from the customer ordering the item to getting it).
DISCOVER THE “FORGOTTEN FUNDAMENTALS” OF OPERATIONS MANAGEMENT”
Our concise video courses here at Rowtons Training offer operations management training to those looking to learn more about business operations, inventory management and much more. Take a look at our Inventory Management A-Z video training course.
If you want to know more, you may find my YouTube video version of this blog article here.
Work In Progress and its effect on Throughput-Time : An Analogy
Consider a private toll road.
- The road is one-way and 10km long.
- The cars driving down the road are the ‘work in progress’ (WIP) of the system.
- Driving down the toll road represents moving through the system.
- Each car wants to get through the system as quickly as possible. (Reduce its “throughput time”)
- The road owner (operations manager) wants to maximise the throughput rate (how many cars get through per hour) of the system, in order to maximise their income.
In Scenario 1, the toll road is very busy and the cars move slowly. In Scenario 2, the toll roll is very quiet and the cars move quickly. However, surprisingly in these (manufactured coincidental but realistic) scenarios, the throughput rate’s (how many cars move through the system per minute) are actually the same!
In the first scenario the cars move at 20km/hr, and so an individual car takes 30 minutes to drive the length of the 10km road. This means that approximately 22 cars per minute get through the toll road.
In the second scenario the cars move at 120km/hr, and so an individual car takes just 5 minutes to drive the length of the same 10km road. However, once again, there is still the same average throughput rate of 22 cars/ minute!
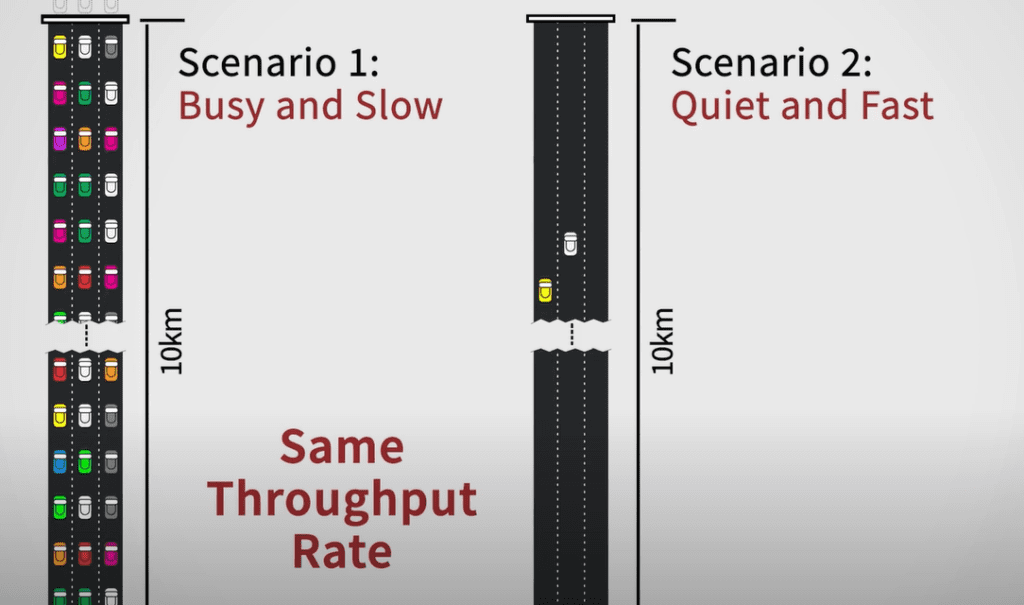
Isn’t that crazy?! Both scenarios have the same throughput rate despite having vastly different throughput times, and the throughput times are directly proportional to the quantity of WIP allowed to be moving through the system.
Going back to previous analogies, the car factory or pizza restaurant might “think” that either scenario of operation is just as good in their business…. The throughput rate (output rate) is the same in both so what’s the problem?
Well, if it is your new custom car crawling along the production line in the car factory for months or “your” pizza you are waiting hours for because the chef is trying to work on too much stuff at the same time, you care A LOT about the throughput-time!
What does this mean for our inventory management and throughput?
Ultimately, certainly pushing more new jobs into your system and increasing the WIP doesn’t guarantee any improvement in the throughput rate. In addition to this, the speed of workflow moving through the system is often less of an operation manager’s choice, but rather a result of decision about WIP inventory you have (or negligently / cluelessly) allow into your system.
Watch the YouTube version of this blog article here on my channel – Laurence Gartside
Little’s Law
Little’s Law is a simple, powerful and very widely applicable formula. It is extensively applicable in operations and inventory management. Little’s Law says that the ‘Level’ (or quantity) of Work-In-Progress inventory is equal to the Throughput-Rate (λ) multiplied by the Throughput Time (W):
L = λW
In Scenario 1, L = is clearly very large. Using Little’s Law, we can calculate it.
Scenario 2 (Quiet and Slow), has a much lower quantity of WIP in its system (fewer cars driving down the road). Although in the graphic we cannot see the full 10km road and count the cars, we can use Little’s Law again to calculate the average L, level / quantity of WIP:
With a driving speed 6x faster, scenario 2 has 6x less WIP (inevitably predictable to all those operations managers who understand Little’s Law).
In both our scenarios the throughput rate, λ, was the same (22cars/ min). This means that the toll road owner (or operations manager) is making the same income from either scenario. However, the customer experience for the drivers on the road is “very” different!
In most business settings, the inventory moving through the system / factory is owned by the business and so the operations manager is more like to care about the quantity of WIP and its throughput time. In our toll road, the short-sighted owner may unfortunately care much less as he only really cares about how many cars he can get through his system. If he fails to realise that its capacity is already constrained at 22 cars/ min, he may be tempted to just shove more jobs into the front of the system (same with a car production line manager or a kitchen chef who keeps accepting more customer orders despite being at their production capacity limit already). But if these systems are already at capacity, they will just increase their customer lead times and have no impact (or maybe even a negative impact on throughput times and therefore customer lead times (from the additional operational complexities).
Optimising Lead Times using Inventory Management
So, our toll road owner sees the light. They realise that pushing more cars onto the toll road is not increasing throughput rate and that all the customers are angry. How can the toll road owner move from scenario 1 to scenario 2, from having a road permanently full of traffic and angry customers with huge lead times, to having the quiet-fast road scenario 2 which causes no loss in throughput-rate?
The answer is highly unintuitive. Temporarily restricting the flow of cars coming onto the road, as a one-time / one-off change will let us create a new steady-state situation (such as scenario 2) where again, the number of cars coming onto the road is equal to the throughput rate of the toll system meaning we can keep our same throughput rate but with dramatically faster throughput times enabled by the reduced WIP moving through the system.
System Work-In-Progress inventory control management is a core area of operations and inventory management with many layers of interlocking complexities. Do it badly and you can piss off all your customers devastating your business. Do it well and you can offer market winning customer delivery lead times, minimising your own operating inventory costs and charging premium prices for your great service. To learn more on the fundamentals of Operations and Inventory Management, take a look at some of the courses on offer from Rowtons Training , for example Inventory Management A-Z, Operations Management A-Z or Lean Manufacturing A-Z .